Machining of Components
Proper machining of FEY rings’ mating components is as critical to the overall sealing effect as the FEY rings themselves. When designing the sealing solution for an application, the mating components should adhere to the following guidelines in order to achieve the best sealing effect possible.
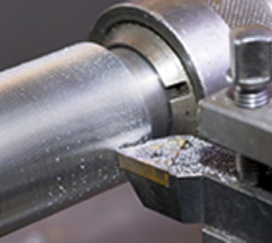
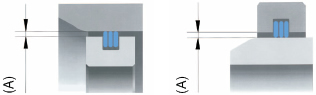
Component Gap
The design for gaps (A) must be as small as possible. The smaller the gap, the better the labyrinth or sealing effect.
Please refer to the information in the respective data sheets for the different ring designs under “Axial and/or radial play” if radial play and/or tilting motions are detected!
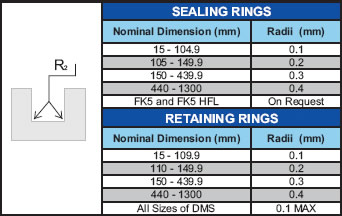
Groove Corner Radii
These charts specify the suggested corner radius in the groove base for selected sealing and retaining ring ranges.
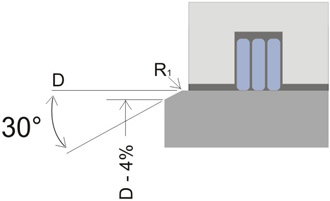
Shaft Chamfer
A 30° max. lead in chamfer, with radius, is needed to aid assembly and avoid damaging the inside clamping FEY rings during assembly. The diameter at the start of the chamfer should be at least 4% smaller that the shaft diameter. The rings expand as they slide over the chamfer and seat at the proper diameter. This allows a tight fit on the shaft once the parts are assembled. Tools to aid installation or special design considerations are highly recommended for shafts with no chamfer.

Bore Chamfer
A 30° max. lead in chamfer, with radius, is needed to aid assembly and avoid damaging the outside clamping FEY rings during assembly. The diameter at the start of the chamfer should be at least 4% larger that the bore diameter. The rings contract as they slide into the chamfer and seat at the proper diameter. This allows a tight fit in the bore once the parts are assembled. Tools to aid installation or special design considerations are highly recommended for shafts with no chamfer.
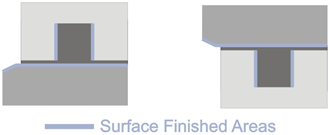
Surface Finish
For most applications, the typical recommended surface finish on surfaces that contact the sealing rings is Ra 3.2. This finish should be applied to the radial walls of the groove as well as the chamfer and surface of the shaft or bore. If your application experiences large axial movement, such as in a hydraulic cylinder, please contact our technical department for surface finish recommendations.